Tegra Gravura Perdizes
Project description
Gravura Perdizes, located in São Paulo’s Perdizes neighborhood, is a residential development by Tegra Incorporadora, executed by Jotawall in partnership with CMC Modular. Featuring 120 prefabricated bathrooms across 18 floors, the project utilized off-site construction to boost efficiency, reduce waste, and minimize on-site labor. This innovative approach shortened timelines, cut fixed costs, and enhanced quality control. Certified by EDGE, it achieves 32% energy efficiency, 21% water savings, and a 30% reduction in embodied energy in materials, showcasing a strong commitment to sustainability and global environmental standards.
Main information
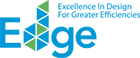
14 444 m²
Multiresidential
building
Tegra
Königsberger
Vannucchi
Contractors
Jota wall
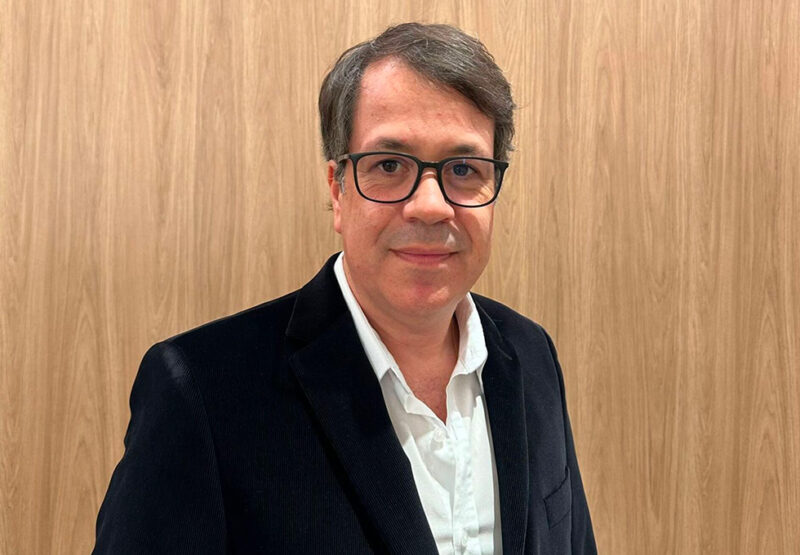
Company name: Jota wall
Main Representative: Juliano Farias
Specialties: Dry construction, construction management
Founded in: 2001
Biography: Jota Wall is a company specialized in dry construction, operating since 2001 and serving the leading players in the national market with drywall systems, monolithic and removable ceilings, acoustic materials, and steel frame.
Innovation Partner: CMC Modular
Website: www.jotawall.com.br
Key Challenges
- Adaptation to a new construction model
Installing 120 ready-made bathrooms across 18 floors required precise coordination among various teams, from manufacturing to installation. - Logistics and on-site integration
Coordinating the delivery and placement of pre-fabricated modules in a space-constrained environment was a challenge, demanding efficient logistics and alignment with the overall project schedule.
Key Achievements
- Innovation through off-site construction
The partnership with CMC Modular Constructions and Jota Wall enabled the use of pre-fabricated bathrooms, reducing execution time, material waste, and the number of workers on-site, while also improving quality control. - Efficiency and cost savings in execution
The industrialization of the process not only shortened the overall project timeline but also lowered fixed costs and increased productivity, proving to be an advantageous solution for future projects.
Sustainability in the project
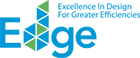
The project earned the prestigious EDGE (Excellence in Design for Greater Efficiencies) certification during the design phase, reaffirming its commitment to sustainable practices. Key highlights include:
32% Energy Efficiency: Reducing energy consumption through innovative solutions and advanced technologies.
21% Water Efficiency: Optimized use of water resources, contributing to environmental preservation.
30% Reduction in Embodied Energy in Materials: Careful selection of materials with lower environmental impact throughout their lifecycle.
- 32% Energy Efficiency: Reducing energy consumption through innovative solutions and advanced technologies.
- 21% Water Efficiency: Optimized use of water resources, contributing to environmental preservation.
- 30% Reduction in Embodied Energy in Materials: Careful selection of materials with lower environmental impact throughout their lifecycle.
This recognition emphasizes the project’s alignment with global sustainability standards, benefiting both residents and the environment